How to Extend the Life of Your Rubber Tracks
Rubber tracks are a great alternative to steel tracks when you want or need to reduce damage to vegetation/soil/asphalt/concrete, reduce noise or provide a smoother ride. And, just like steel tracks, rubber tracks will last longer if used appropriately and are properly maintained.
Here are five tips for increasing the life of your tracks:
- Use them only in appropriate applications
Each track has a tread profile, which helps the track work well in some conditions, but all treads have drawbacks. The most popular tread patterns include the C-lug tread, the staggered tread, the straight-bar tread and the multi-bar tread. The C-lug tread works well in both on- and off-road applications; it also boasts a smooth ride. The staggered tread is well-suited for abrasive surfaces, provides a comfortable ride on hard surfaces and decreases ground disturbance. The straight-bar tread is designed for muddy, wet terrain and is considered to be a very “aggressive” track. The multi-bar tread works well on loose ground and on hard surfaces.
- Proper machine operation decreases wear
Operating a machine in an improper manner increases wear and has potential safety risks. Even operating in an aggressive manner can accelerate wear. Any operation that requires a machine (or its components) to work outside of its specifications, puts undue stress on it, so it is imperative to operate equipment properly.
Some tasks—although not necessarily improper or aggressive—can still have a negative impact on the integrity and longevity of your tracks. Counter-rotations or sharp changes of direction, for example, can greatly contribute to accelerated wear of the tracks. The amount of damage increases when traveling on highly abrasive material, such as shale, granite or ragged materials commonly found on demolition sites. Also, when tracks spin, they experience greater wear.
- Perform regular inspections
Prior to operation, the operator should check the machine, including its tracks. Tracks should be inspected daily for signs of damage, such as rubbing, cracking, stretching and UV damage. Also look for dirt or debris and remove it, since dirt and debris can prevent an undercarriage from functioning properly and this puts undue stress on effected components.
Tracks should be examined weekly for proper tension. Improper tension is a major contributor of premature track failure. Also examine other undercarriage components for signs of wear.
Once tracks surpass their expected half-life, the thickness of the rubber should be examined monthly to determine how much life is left in them.
Pivot Provides Cost-Effective Quality Choice for Undercarriage Replacement
“Pivot Provides Cost-Effective Quality Choice for Undercarriage Replacement”
- Keep tracks clean
It is wise to clean the tracks at the end of the day, but cleaning will probably need to be completed more frequently than that. The frequency will depend on the environment and application. It is good practice to check the tracks for dirt and debris any time the operator gets out of the cab or has a break.
Give extra attention to the front and rear roller wheels, since this is where material tends to accumulate. Use a shovel or pressure washer to remove debris. Sharp rocks, rebar, concrete, scrap metal and other demolition material cause greater damage than most other materials. Metal wire can wrap around the tracks.
Also, ensure the work area is cleared of unnecessary debris; this will help prevent it from getting into the tracks or possibly damaging them.
- Maintain your tracks like you want them to last
If an operator in the field identifies a problem with the tracks, respond appropriately. Purchase new parts. Make arrangements to take the machine out of the field. Address the issue and get the machine back into the field. Consider component life expectancies as dictated by the manufacturer and the application in which the machine is operating as well as how it is being operated in order to plan for downtime. By planning your maintenance schedule as opposed to just reacting to what is happening, you can prevent premature failure.
Tracks will eventually fail but, by taking these steps, you can address issues before they become problems, thereby increasing the life of your tracks.
Searching For Heavy Equipment Parts?
We specialize in undercarriage and complete components for excavators, dozers, crawler loaders, and wheel loaders.
Searching For Heavy Equipment Parts?
We specialize in undercarriage and complete components for excavators, dozers, crawler loaders, and wheel loaders.
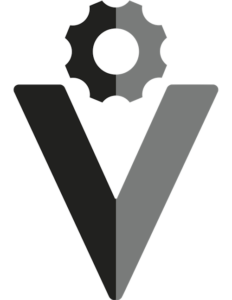